How to best replace steel bends with wear resistant HDPE
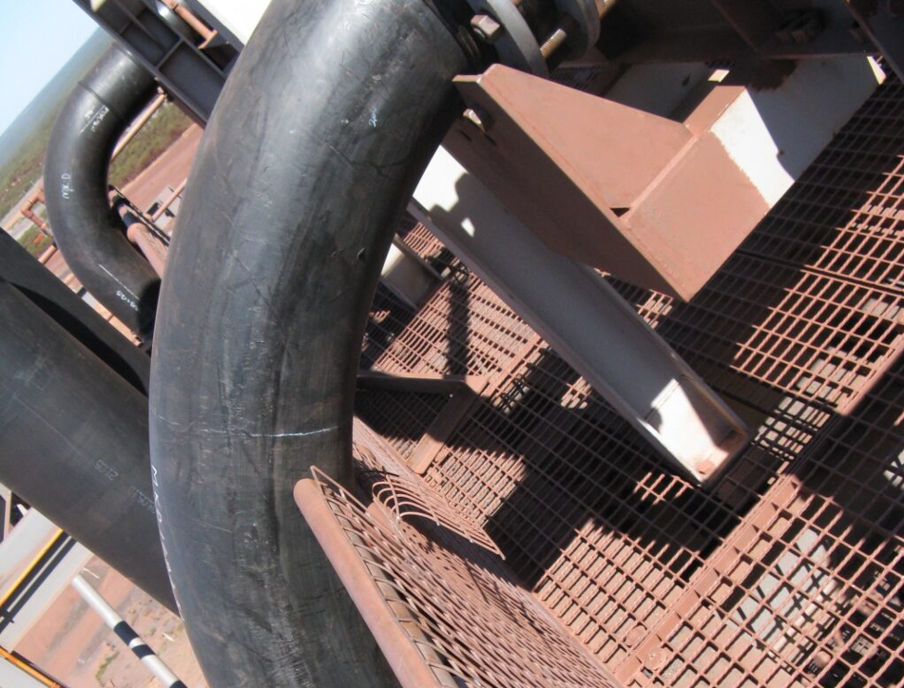
Image: Highlighting the challenge of fitting a 3D bend, this photo shows a modified guardrail to accommodate it. Contrastingly, the 1.5D bend behind seamlessly fits in the same position, offering optimal performance without altering the guardrail.
We recently received a customer query about how to get HDPE bends to match steel long radius dimensions.
The customer wanted to use HDPE but had experienced real problems in the past when it came to fitting in the huge sweep bends – or Long Radius Bends as they’re known in the steel industry – as a replacement for steel pipe.
This is absolutely possible, it’s just about ensuring the size is correct. 15 years ago, sweep bends in HDPE were only available in 3D Radius as this is the easiest dimension to form bends made from poly pipe. In steel they are mandrel bent to 1.5Dso to bend HDPE pipe to 1.5D whilst maintaining pipe wall thickness integrity requires a lot of technology and expertise.
3D vs 1.5D
HDPE can replace steel V bends but not directly, as HDPE 3D bends are slightly too large for steel pipes.
That’s why we replace them with a HDPE 1.5D bend, as they’re more compact and provide the same size with better performance as a steel bend.
We recommend using HDPE 1.5D bends as a lot of other products on the market taper out, becoming thinner and more fragile at the back which makes it impossible to achieve a good weld when cutting into the radius.
Due to the consistency of the wall thickness of HDPE 1.5D bends, Advanced Piping Systems are able to cut and trim the angle needed to whatever size is required for any steel pipe replacement application.
Cutting back sweep bends
We know that some of our customers trim their 3D sweep bends when the Spigot leg is too long in order to make the model fit, this becomes an issue if you cut back into the radius, as this changes the angle and makes it very difficult to weld on the stub end. Also the pipe dimensional tolerances can be way out and not provide the required pressure rating required.
If you are using 3D, you can alleviate this issue, by leaving 100mm of spigot after the radius.
Having said that, this is only a problem with 3D bends, which is why we recommend 1.5D, as it’s a better quality bend.
Fabricate to any requirements
At Advanced Piping Systems, we can provide all angles and sizes of HDPE pipe, including 3D & 5D if required but find that the HDPE 1.5D bends are superior to fabricate with and won’t relax like 3D bends in the open environment. This is because the manufacturing process in making 1.5D breaks the HDPE pipe memory more completely.
We have the capability in-house to fabricate any size you need to fit your specific requirements and carry substantial stock, so if you come across tricky bends our friendly customer service team is here to help in a timely manner.
The client was also happy to discover we had his product in stock. We maintain a substantial stock of most products within standard size ranges and our recently updated website provides live stock updates, allowing you to locate your required parts and obtain real-time information on their availability, ensuring transparency in the process.
Click here to request a quote or to find out more about sweep bend fittings.